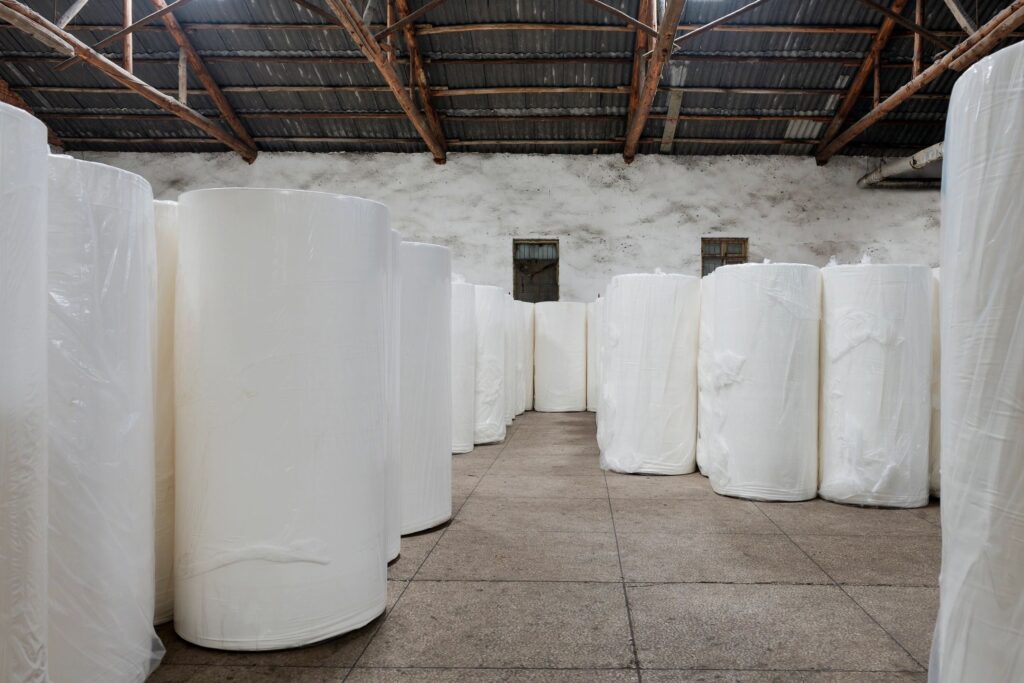
In the bustling world of the pulp and paper industry, efficiency is the name of the game. From manufacturing to packaging, every step in the process demands meticulous attention to detail to ensure high-quality output while minimizing costs and environmental impact. One critical component in this equation is oxygen gas, which plays a multifaceted role in various stages of production. In recent years, the adoption of on-site oxygen gas generating systems has emerged as a game-changer, offering unprecedented benefits in terms of cost reduction, operational efficiency, and sustainability.
The role of oxygen gas in pulp & paper production:
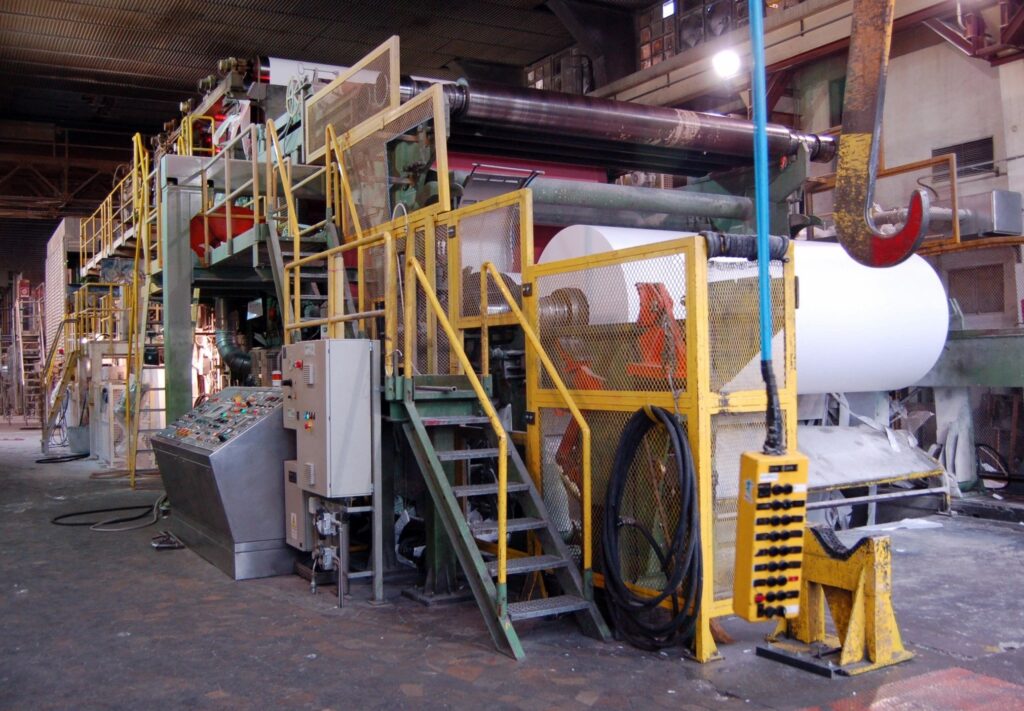
Oxygen gas serves several indispensable functions within the pulp and paper manufacturing process. One of its primary applications is in bleaching, where it is used to remove color from pulp fibers, resulting in bright, white paper products. Oxygen delignification, a key step in the bleaching process, relies on the oxidative power of oxygen gas to break down lignin—a complex organic polymer found in wood fibers—without the need for environmentally harmful chlorine-based chemicals. Additionally, oxygen is utilized in wastewater treatment processes to enhance the degradation of organic pollutants, promoting environmental stewardship and regulatory compliance.
Challenges with traditional oxygen supply methods:
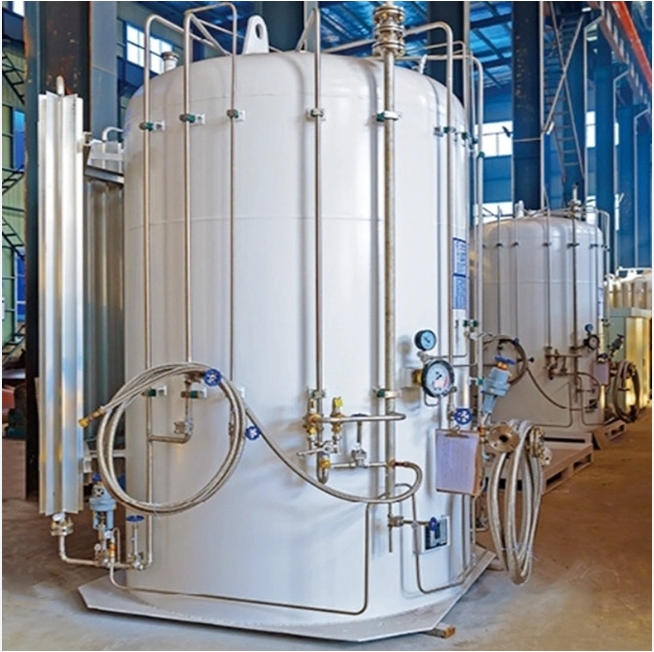
BULK LIQUID OXYGEN TANK
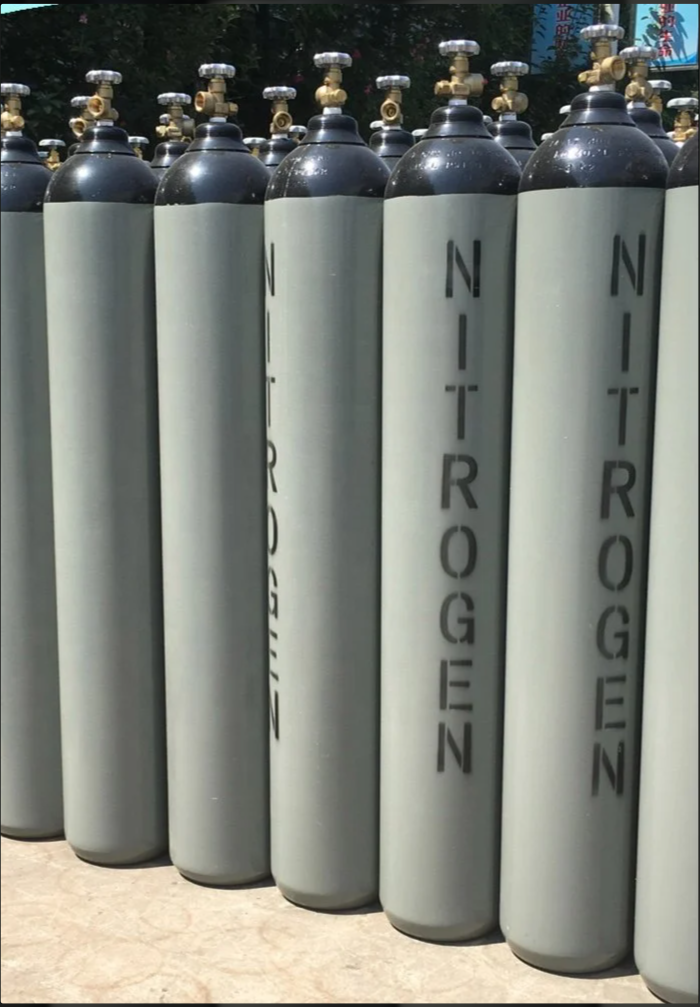
HIGH-PRESSURE OXYGEN CYLINDER
Historically, pulp and paper mills have relied on traditional methods of oxygen supply, such as cryogenic distillation or oxygen cylinders delivered from off-site suppliers. While effective, these methods present several drawbacks. Cryogenic distillation, for instance, requires large-scale infrastructure and significant energy consumption, making it less economically viable for smaller operations. On the other hand, reliance on oxygen cylinders entails logistical challenges, including transportation costs, storage space requirements, and supply chain vulnerabilities.
The arrival of on-site oxygen gas generating systems:
Recognizing the limitations of conventional oxygen supply methods, many pulp and paper manufacturers have turned to on-site oxygen gas generating systems as a more sustainable and cost-effective alternative. These systems utilize advanced technologies, such as pressure swing adsorption (PSA) or vacuum pressure swing adsorption (VPSA), to extract oxygen from ambient air, purify it to industrial-grade standards, and deliver it directly to the point of use.
Advantages of on-site oxygen generation:
Cost Reduction: By eliminating the need for bulk oxygen deliveries and associated transportation expenses, on-site oxygen generation significantly reduces operational costs over time. Moreover, the scalability of these systems allows mills to adjust oxygen production according to fluctuating demand, further optimizing resource utilization.
Operational Efficiency: On-site oxygen generation systems offer greater reliability and flexibility compared to traditional supply methods. With continuous oxygen availability on-site, mills can streamline production schedules, minimize downtime, and maintain consistent product quality, thereby enhancing overall operational efficiency.
Environmental Sustainability: By producing oxygen on-site from ambient air, manufacturers can substantially reduce their carbon footprint and environmental impact. Unlike cryogenic distillation, which consumes large quantities of energy and emits greenhouse gases, on-site oxygen generation systems operate with greater energy efficiency and generate minimal waste, aligning with sustainability objectives.
Supply Chain Resilience: In an increasingly interconnected global economy, disruptions to supply chains can pose significant challenges to business continuity. On-site oxygen generation empowers pulp and paper mills to enhance their resilience by reducing dependency on external suppliers and mitigating risks associated with supply chain disruptions, such as transportation delays or shortages.
In the dynamic landscape of the pulp and paper industry, innovation is paramount to success. On-site oxygen gas generating systems represent a paradigm shift in oxygen supply management, offering a compelling combination of cost savings, operational efficiency, and environmental sustainability. As more manufacturers embrace this transformative technology, the industry as a whole stands to benefit from enhanced competitiveness, resilience, and stewardship of natural resources. Through strategic investments in on-site oxygen generation, pulp and paper mills can chart a course toward a brighter, more sustainable future.
Enquire Now
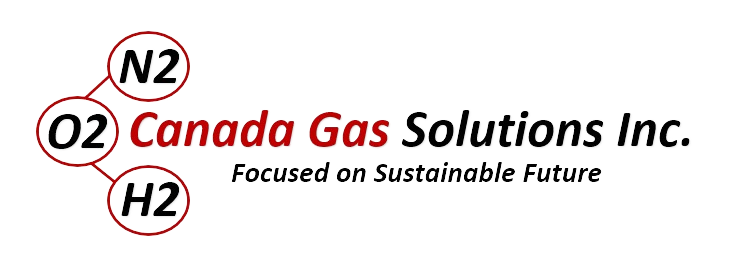