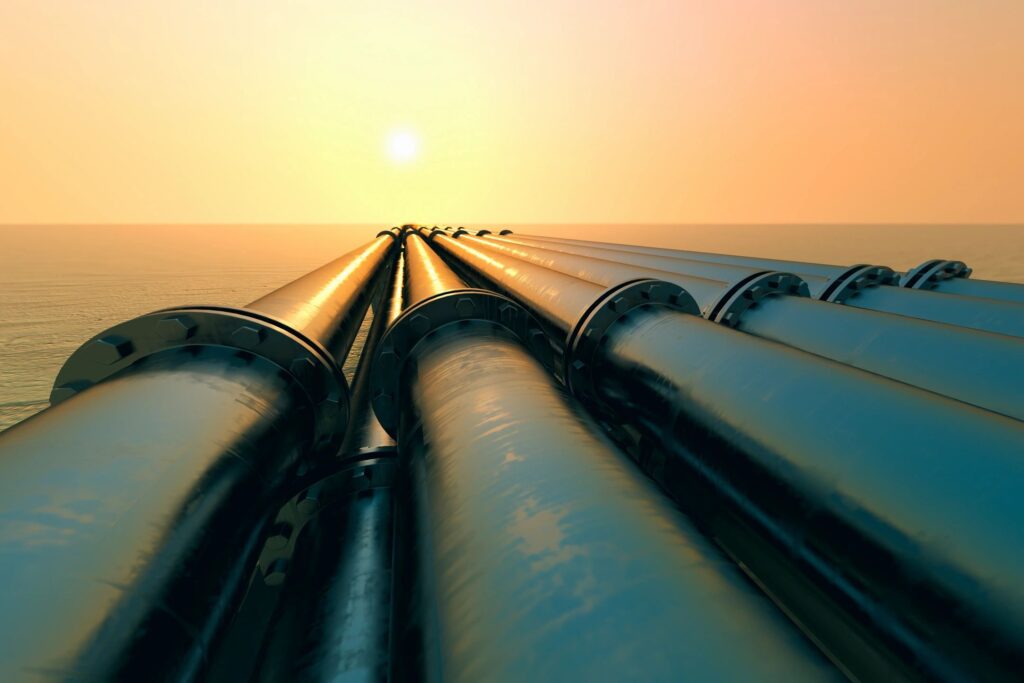
In the intricate network of oil and gas pipelines, ensuring smooth operation and safety is paramount. One of the key techniques employed in pipeline maintenance is pigging and purging, which involves the use of a specialized device called pig and gases to clean and maintain pipelines. Among these gases, nitrogen has emerged as a versatile and efficient option, especially when produced onsite through nitrogen gas generating systems. Let’s understand the significance of pipeline pigging and purging, along with the advantages of utilizing onsite nitrogen generation in the oil and gas industry.
PIPELINE PIGGING & PURGING: ENSURING EFFICIENCY AND SAFETY

Pipelines in the oil and gas industry are prone to the accumulation of various substances over time and these accumulations can impede the flow of products, increase operational costs, and pose significant safety risks. To mitigate these issues, pipeline pigging and purging are employed as preventive maintenance techniques.
Pigging involves the use of a pig launcher, receiver & pig which are connected to the pipeline and propelled by the flow of product or by external means. These pigs effectively scrape and clean the inner walls of the pipeline, removing debris and buildup. Purging, on the other hand, entails the displacement of unwanted substances, such as oxygen, moisture, and hydrocarbons, from the pipeline by introducing inert gases like nitrogen.
THE ROLE OF NITROGEN GAS IN PIPELINE MAINTENANCE
Nitrogen gas has gained widespread acceptance in the oil and gas industry for various applications, including pipeline pigging & purging, due to its inert properties and ability to displace other gases effectively. When used for purging, nitrogen creates an oxygen-free environment, reducing the risk of corrosion, combustion, and contamination within the pipeline. Additionally, nitrogen can be utilized to pressure test pipelines, ensuring structural integrity and leak prevention.
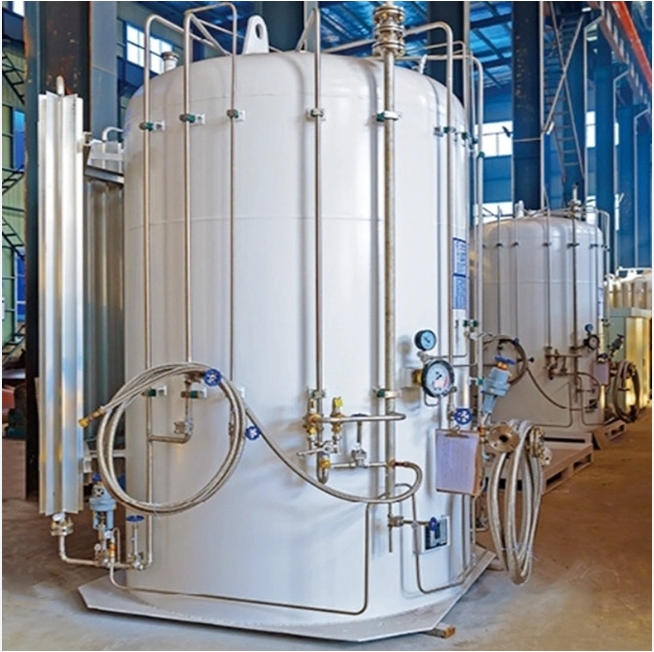
LIQUID NITROGEN TANK
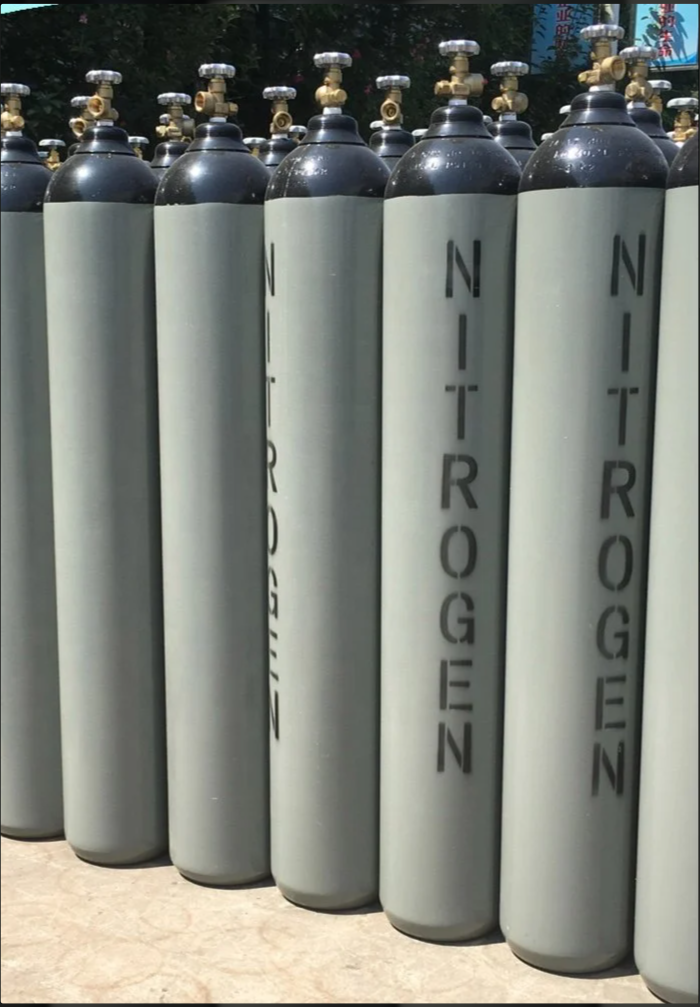
COMPRESSED NITROGEN GAS CYLINDERS
Traditionally, nitrogen for pipeline purging and other industrial applications was sourced from bulk liquid nitrogen suppliers or delivered in high-pressure cylinders. However, these methods come with logistical challenges, transportation costs, and dependency on external suppliers, leading to increased operational expenses for oil and gas companies.
ON-SITE NITROGEN GAS GENERATION: A COST-EFFECTIVE SOLUTION
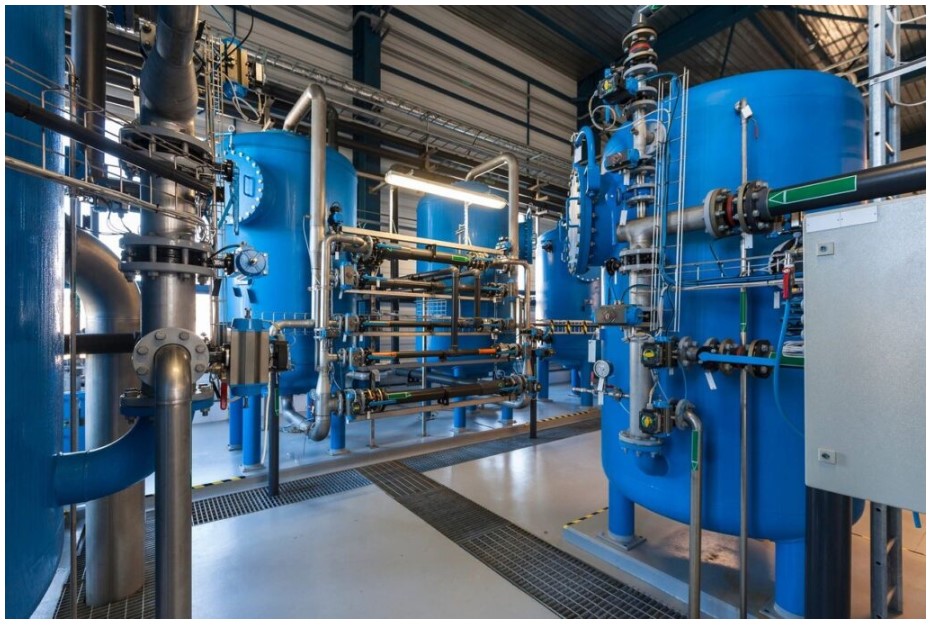
STATIONARY ON-SITE NITROGEN GAS GENERATING SYSTEM
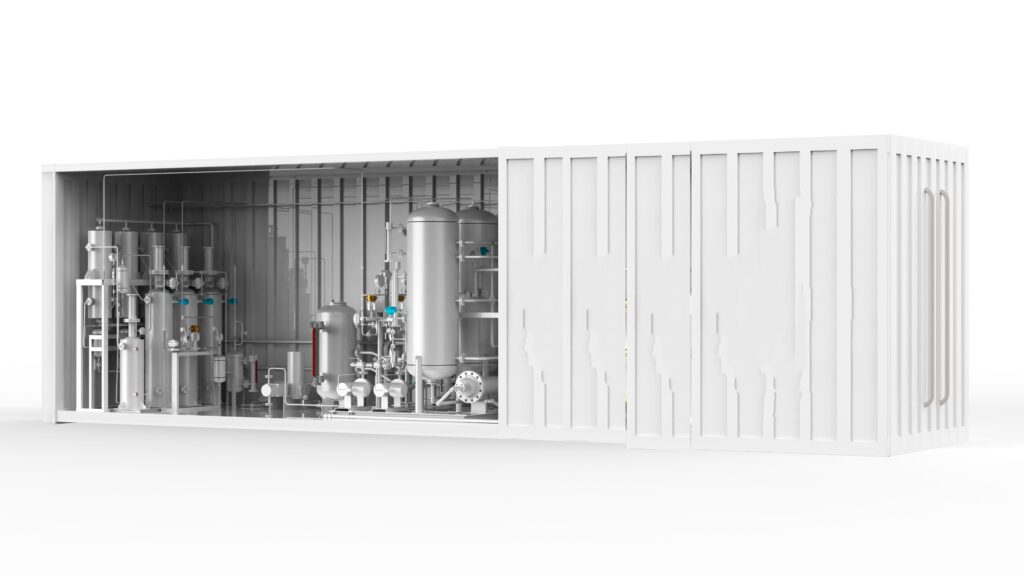
CONTAINERIZED MOBILE NITROGEN GAS GENERATING SYSTEM
Onsite nitrogen gas generation systems offer a cost-effective and efficient alternative to traditional nitrogen supply methods. These systems utilize pressure swing adsorption (PSA) or membrane separation technology to extract nitrogen from the ambient air, providing a continuous and reliable source of high-purity nitrogen on-site.
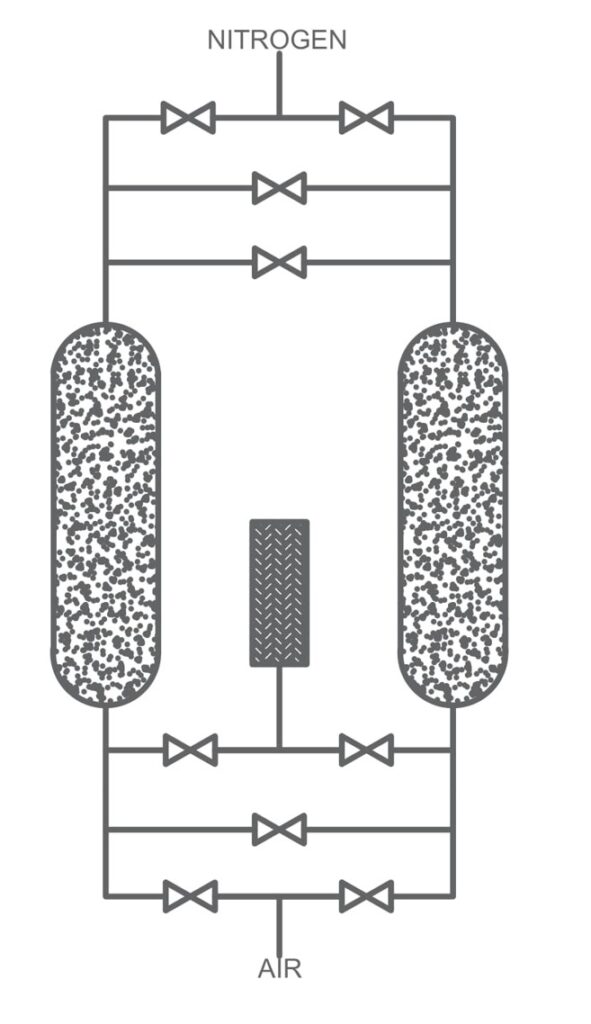
NITROGEN GENERATION USING PRESSURE SWING ADSORPTION TECHNOLOGY
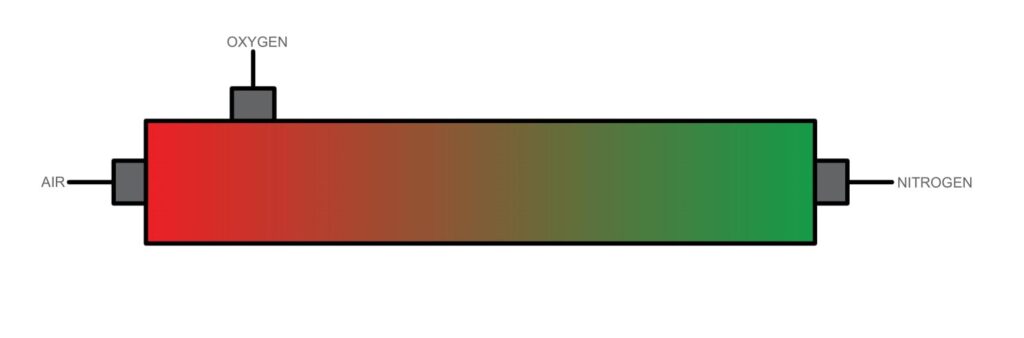
NITROGEN GENERATION USING MEMBRANE TECHNOLOGY
The Adoption of on-site nitrogen generation offers several advantages for the oil & gas industry:
Cost Savings: By producing nitrogen on-site, companies can eliminate transportation and delivery costs associated with bulk liquid nitrogen or cylinder rentals. Moreover, the operational expenses are significantly reduced over time, as there is no reliance on external suppliers.
Increased Operational Efficiency: Onsite nitrogen generation systems provide a continuous supply of nitrogen, allowing for immediate access whenever needed. This eliminates delays associated with scheduling deliveries or waiting for cylinder replacements, thereby enhancing operational efficiency.
Customization & Scalability: Onsite nitrogen generation systems can be tailored to meet specific production requirements and scaled according to the size and scope of the operation. Whether for large-scale pipeline projects or smaller maintenance tasks, these systems offer flexibility and adaptability.
Environmental Sustainability: By generating nitrogen on-site, companies reduce their carbon footprint associated with transportation and logistics. Additionally, onsite generation eliminates the need for energy-intensive processes required for the liquefaction and transportation of bulk nitrogen.
In conclusion, pipeline pigging, purging, and maintenance are critical aspects of ensuring the integrity, efficiency, and safety of oil and gas infrastructure. By leveraging the inert properties of nitrogen gas and adopting onsite generation technology, companies can streamline their maintenance processes, reduce operational expenses, and enhance overall productivity. As the industry continues to prioritize cost-effectiveness and sustainability, onsite nitrogen generation emerges as a strategic solution for optimizing pipeline operations.
Enquire Now
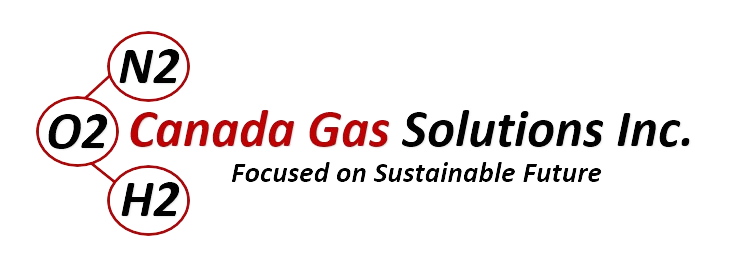