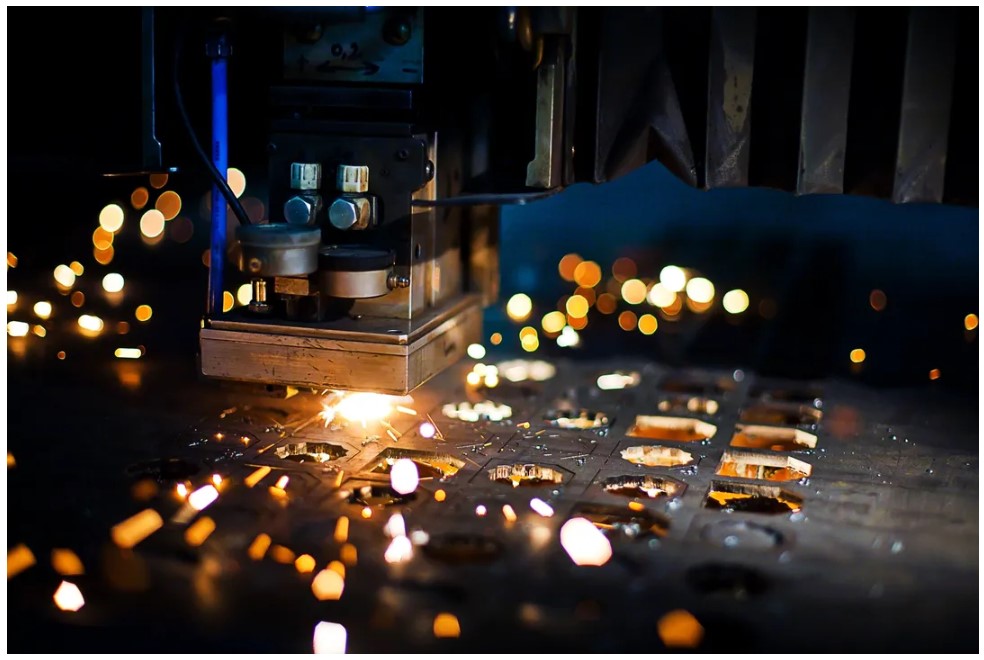
Laser cutting has become an essential tool for industries requiring precise, high-quality cuts on metals such as aluminum, mild steel, and stainless steel. Central to this process is the use of high-pressure nitrogen gas, which enhances cut quality by preventing oxidation, enabling smoother edges, and ensuring a polished finish. While traditional nitrogen supply methods like high-pressure cylinders or liquid nitrogen tanks have been the norm, onsite gas generation systems are redefining how manufacturers approach gas supply, offering unmatched efficiency and cost savings.
WHY HIGH-PRESSURE NITROGEN GAS IS ESSENTIAL FOR LASER CUTTING :
In laser cutting, high-pressure nitrogen gas serves as a shielding agent that displaces oxygen around the cut area. This prevents oxidation, improves cut quality, and maintains the metal’s physical and aesthetic properties.
- Aluminum Cutting:
Nitrogen ensures a clean, reflective finish by eliminating oxidation, which is critical for applications in automotive, aerospace, and electronics industries. - Mild Steel Cutting:
While oxygen is often used for speed, nitrogen is preferred when oxide-free, high-quality edges are required for parts undergoing additional treatments or used in visible applications. - Stainless Steel Cutting:
Nitrogen prevents discoloration and preserves the material’s corrosion resistance, making it ideal for decorative and structural uses.
ONSITE NITROGEN GENERATORS: THE FUTURE OF GAS SUPPLY
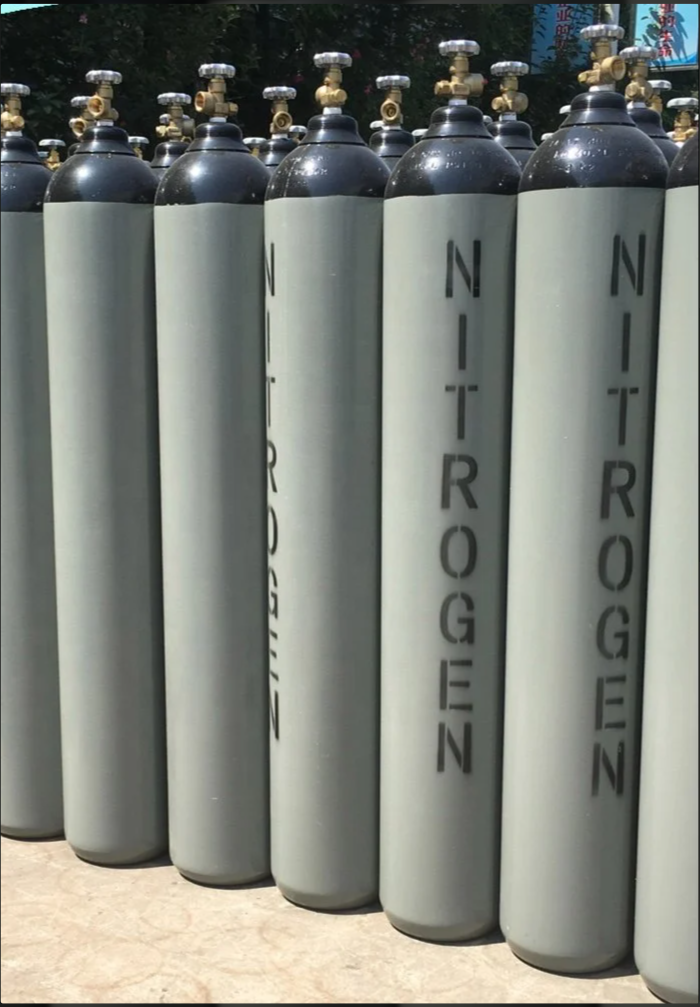
HIGH PRESSURE N2 CYLINDERS
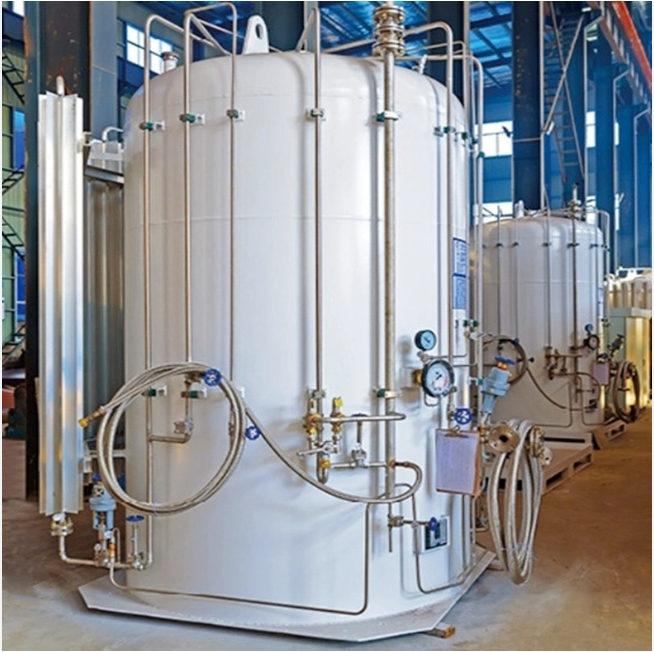
LIQUID NITROGEN TANK
Traditional nitrogen supply methods, such as high-pressure cylinders or liquid nitrogen tanks, come with several challenges: high costs, logistical complexities, and potential supply disruptions. Onsite nitrogen generation systems offer a transformative alternative, producing high-pressure nitrogen gas directly at the point of use.
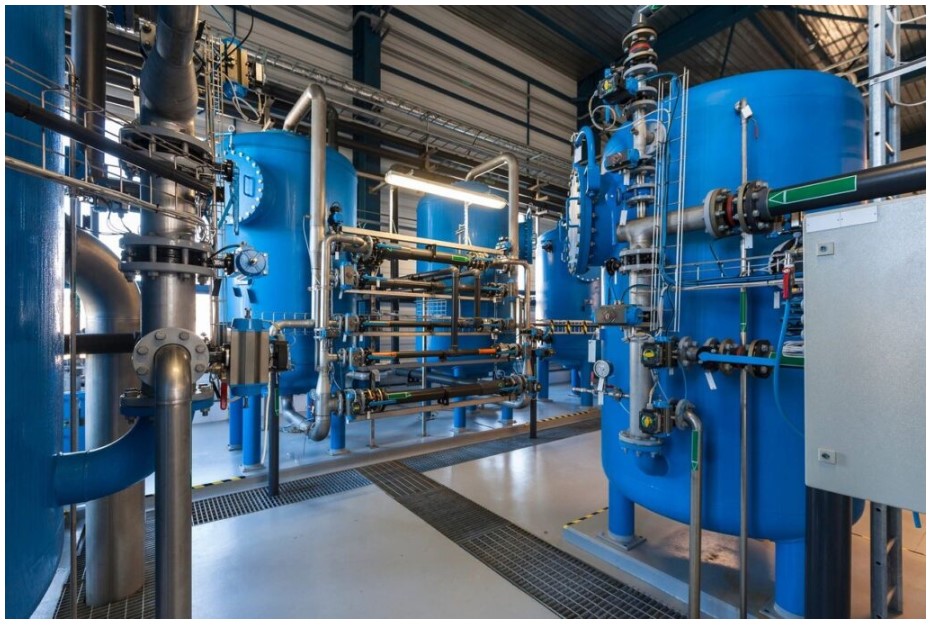
ONSITE NITROGEN GAS GENERATOR
Benefits of Onsite Nitrogen Gas Generators:
- Unmatched Cost Savings:
By eliminating recurring expenses for transport, cylinder handling, and storage, manufacturers can save up to 90% on nitrogen costs. - Customizable Pressure and Purity:
Advanced generators provide nitrogen at pressures and purities tailored to specific cutting needs, ensuring optimal performance for aluminum, mild steel, and stainless steel. - Consistent Supply:
Onsite systems ensure a continuous flow of nitrogen gas, eliminating the downtime risks associated with delayed cylinder deliveries or empty tanks. - Reduced Environmental Impact:
Onsite generation reduces the carbon footprint associated with the transportation and storage of nitrogen, aligning with sustainability goals.
CANADA GAS SOLUTIONS: TAILORING NITROGEN SUPPLY FOR YOUR LASER CUTTING NEEDS:
At Canada Gas Solutions, we understand the critical role that high-pressure nitrogen gas plays in achieving precise, high-quality cuts in metal fabrication. Our team works closely with manufacturers to assess their laser cutting requirements and recommend nitrogen purity levels to meet specific cut quality standards.
Whether you’re cutting aluminum, mild steel, or stainless steel, we provide tailored solutions with onsite nitrogen gas generators that deliver unmatched cost savings, efficiency, and reliability. Say goodbye to the hassles of cylinder management or liquid nitrogen tanks—our systems ensure you have the right purity and pressure of nitrogen gas whenever you need it.
Enquire Now
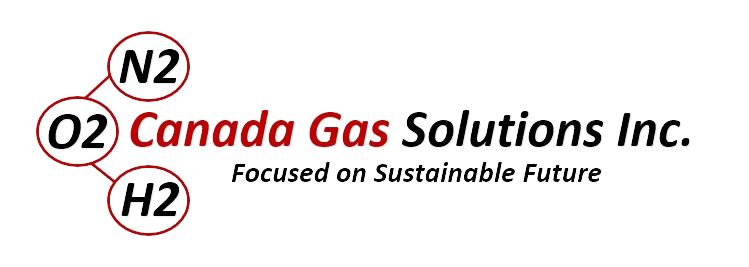