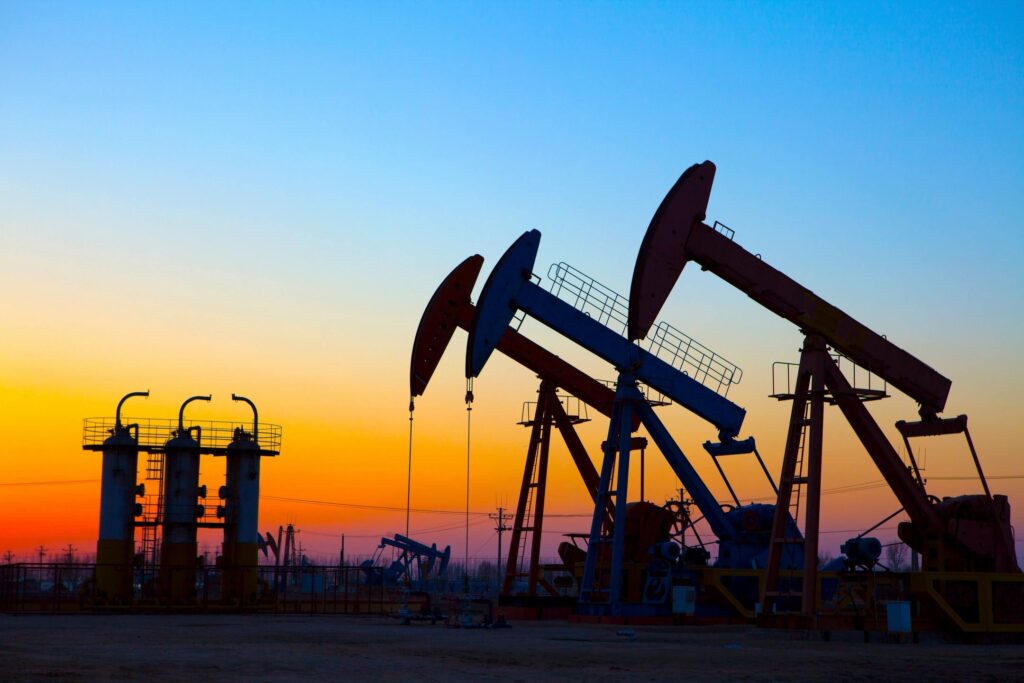
In the field of the oil and gas industry, efficiency, safety, and cost-effectiveness are paramount. Nitrogen gas plays a crucial role in the oil and gas sector, particularly in processes such as blanketing, purging, and inerting. As technology advances, companies are continually seeking innovative solutions to enhance their operations while mitigating risks and reducing expenses. One such advancement that has gained significant traction in Upstream, Midstream & Downstream sectors is the utilization of on-site nitrogen gas generators. These systems offer a plethora of benefits, ranging from enhanced safety measures to substantial cost savings, making them a valuable asset in various oil and gas applications.
THE OIL AND GAS INDUSTRY BENEFITS IMMENSELY FROM THE ADOPTION OF ON-SITE NITROGEN GAS GENERATORS ACROSS VARIOUS APPLICATIONS:
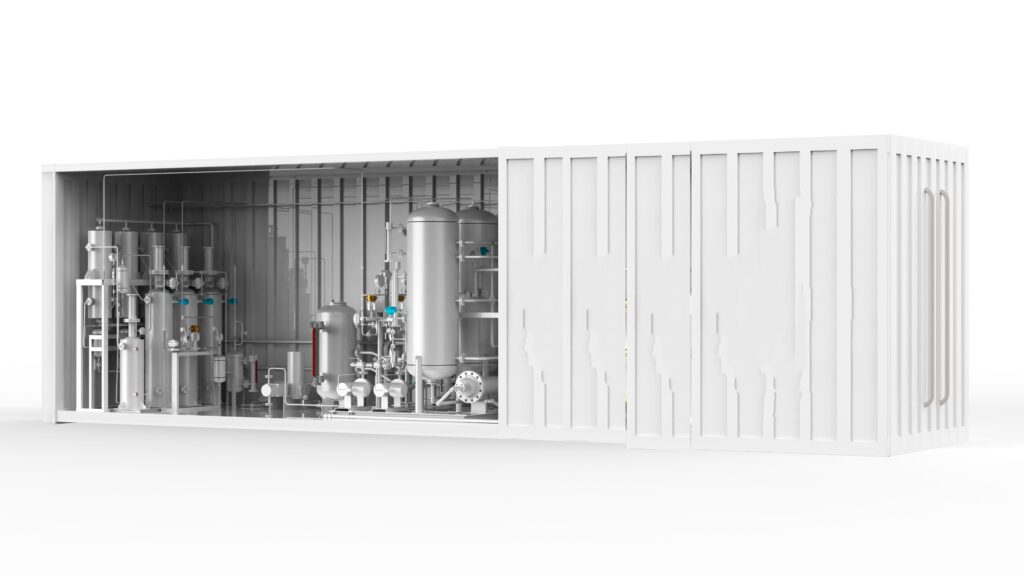
MOBILE CONTAINERIZED ON-SITE NITROGEN GAS GENERATOR
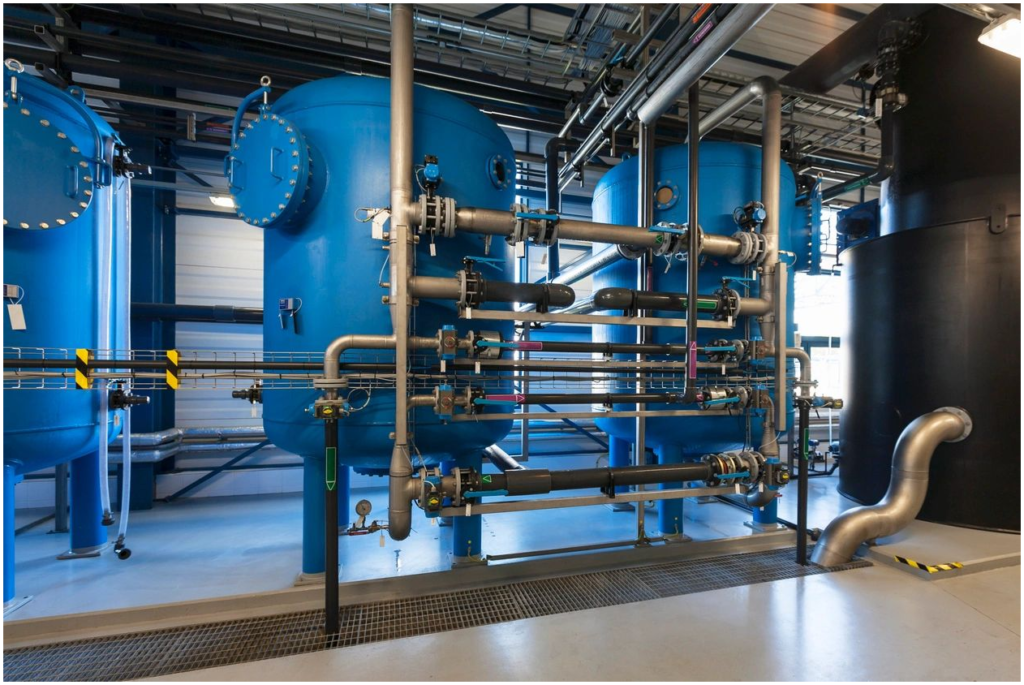
STATIONARY ON-SITE NITROGEN GAS GENERATOR
Versatility in Applications: On-site nitrogen generators find applications across various segments of the oil and gas industry, including well drilling, pipeline purging, pressure testing, blanketing, and enhanced oil recovery (EOR) operations. Their versatility allows companies to address a wide range of nitrogen requirements across different stages of the production process, thereby optimizing efficiency and performance.
Enhanced Safety: Safety is paramount in the oil and gas sector, where operations often involve hazardous materials and environments. On-site nitrogen generators reduce safety risks associated with the transportation, handling, and storage of nitrogen cylinders or tanks. With nitrogen produced on-site, the potential for accidents during transportation or storage is significantly minimized, ensuring a safer work environment for personnel.
Increased Operational Efficiency: On-site nitrogen generators offer a dependable source of nitrogen gas, eliminating delays caused by supply chain disruptions or depleted nitrogen cylinders or liquid tanks. This ensures uninterrupted operations, minimizing downtime and optimizing productivity. Additionally, these generators can be customized to meet specific flow rate and purity requirements, providing flexibility to adapt to varying operational demands.
Environmental Sustainability: On-site nitrogen generators promote environmental sustainability by reducing the carbon footprint associated with transportation and distribution of nitrogen. By generating nitrogen gas on-site using air as the feedstock, companies can minimize greenhouse gas emissions and decrease reliance on fossil fuel-based transportation, aligning with sustainability goals and regulatory requirements.
Cost Savings: Cost considerations are a crucial factor for any business, and the oil and gas industry is no exception. On-site nitrogen generation offers substantial cost savings compared to traditional nitrogen supply methods. By eliminating recurring rental fees, delivery charges, and bulk nitrogen purchase costs, companies can achieve significant reductions in their nitrogen-related expenses over time, resulting in improved bottom-line profitability.
Enquire Now
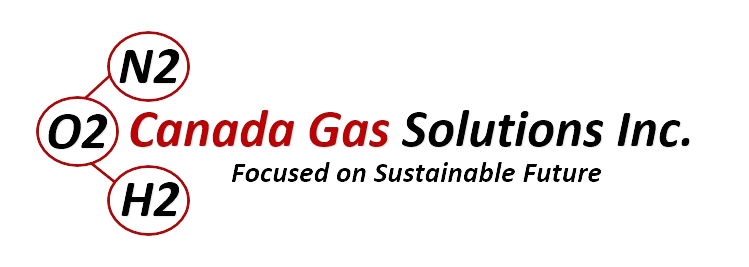