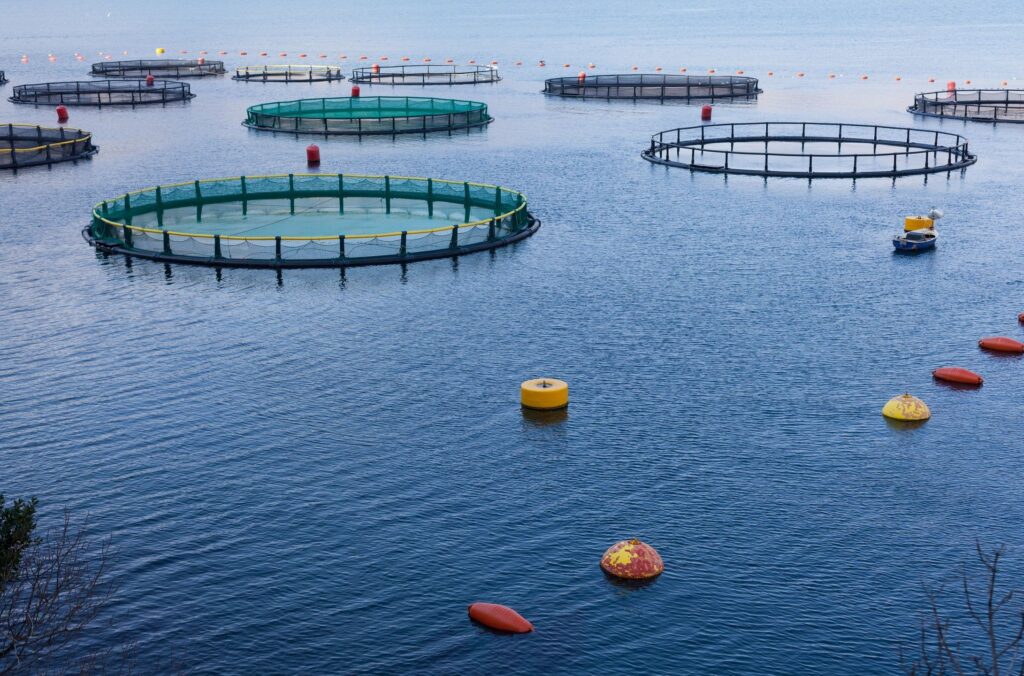
Aquaculture industry, where the delicate balance of water quality directly influences the health and growth of aquatic organisms, the role of oxygen gas cannot be emphasized enough. Oxygen is not only essential for the respiration of fish but also plays a crucial role in maintaining optimal water quality parameters. The strategic use of oxygen gas in fish farming and aquaculture represents a cornerstone of modern aquaculture practices. By ensuring adequate oxygenation, fish farmers can create optimal conditions for fish growth, health, and overall farm productivity. As the aquaculture industry continues to expand to meet growing global demands for seafood, the effective management of dissolved oxygen levels will remain paramount in ensuring the sustainability and success of fish farming operations.
The importance of Oxygen in Aquaculture:
Oxygen is fundamental for the survival of all aquatic organisms, including fish. In a closed aquaculture system, such as tanks or ponds, the dissolved oxygen (DO) levels can fluctuate due to various factors, including stocking density, temperature, and organic load. Insufficient oxygen levels can lead to stress, reduced growth rates, and increased susceptibility to diseases among fish populations. By supplementing oxygen gas into the aquaculture system, farmers can actively manage and optimize DO levels, thereby enhancing the overall health and productivity of their fish stocks. This proactive approach not only mitigates the risks associated with oxygen depletion but also creates an environment conducive to improved feed conversion rates and accelerated growth.
Techniques for oxygenation in Aquaculture:
Several techniques are employed to introduce oxygen gas into aquaculture systems, ranging from simple aeration to sophisticated oxygenation systems. Aeration, which involves the agitation of water to facilitate gas exchange at the water surface, is commonly used in small-scale operations and extensive pond systems. In contrast, more advanced methods such as oxygen injection systems utilize specialized equipment to directly infuse oxygen gas into the water column, ensuring precise control over dissolved oxygen levels. These systems offer greater efficiency and flexibility, particularly in intensive recirculating aquaculture systems (RAS) where space and water quality management are critical.
Some of the Fish Breeds Benefitting from Oxygenation:
Various fish breeds exhibit enhanced growth rates, improved feed conversion efficiencies, and overall better health outcomes when reared under oxygen-enriched conditions. Some notable species that particularly benefit from oxygenation in aquaculture include:
Trout: Cold-water species like trout require well-oxygenated water to thrive. Oxygen supplementation becomes crucial, especially in intensive farming systems where water temperatures may rise, leading to decreased oxygen solubility.
Salmon: Salmon farming, particularly in RAS facilities, relies heavily on oxygenation to maintain water quality and support the high stocking densities characteristic of intensive production systems.
Tilapia: Tilapia are highly adaptable and fast-growing fish commonly cultivated in aquaculture. Optimal oxygen levels are essential for maximizing their growth potential and minimizing stress-related issues.
Catfish: Species such as channel catfish are popular choices in aquaculture due to their rapid growth and tolerance to a wide range of environmental conditions. Oxygenation ensures optimal growth rates and reduces the risk of disease outbreaks.
on-site oxygen gas generating systems are transforming aquaculture practices:
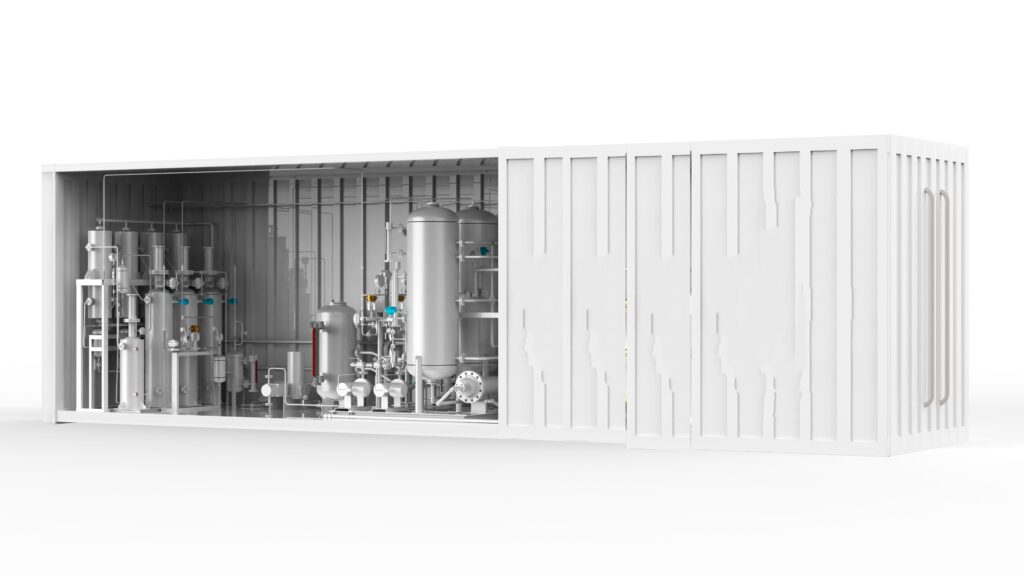
MOBILE CONTAINERIZED OXYGEN GAS GENERATING SYSTEM

STATIONARY OXYGEN GAS GENERATING SYSTEM
On-site oxygen gas generators are revolutionizing the aquaculture industry by providing a reliable and cost-effective solution to oxygen supplementation. These generators utilize advanced PSA or VPSA technologies to produce oxygen gas directly at the aquaculture facility, eliminating the need for transportation and storage of oxygen cylinders or liquid bulk tanks. By generating oxygen on demand, fish farmers can ensure a continuous and consistent supply of oxygen to their fish tanks or ponds, regardless of location or infrastructure constraints. This flexibility enables aquaculture operations to optimize oxygen levels based on real-time monitoring, resulting in improved water quality, enhanced fish health, and increased production efficiency. Furthermore, on-site oxygen generation reduces reliance on external suppliers, mitigates logistical challenges, and lowers operational costs, making it a sustainable and environmentally friendly choice for modern aquaculture facilities.
Enquire Now
