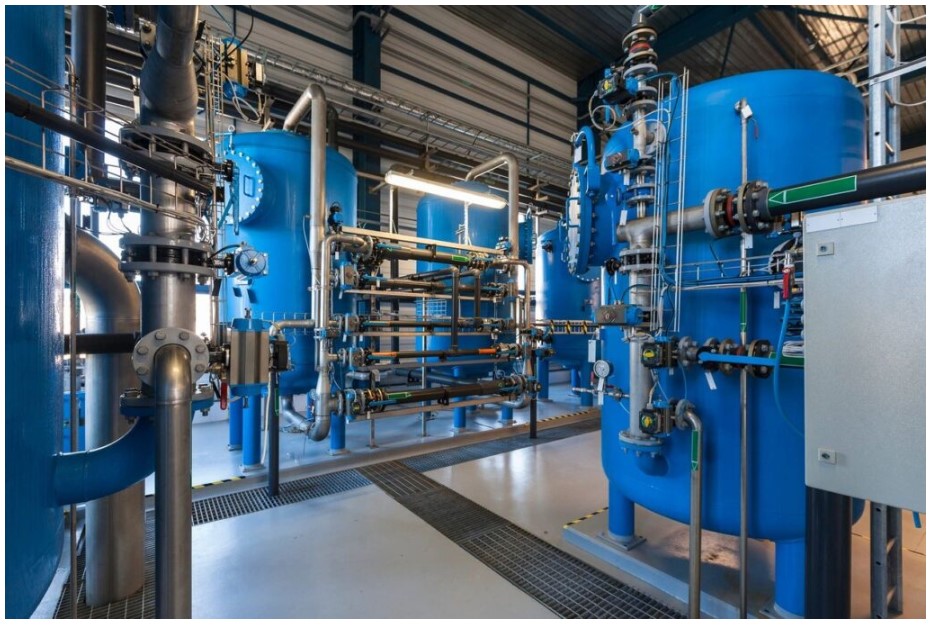
In industries where a reliable source of nitrogen gas is crucial, on-site nitrogen gas generators have emerged as indispensable assets, offering a cost-effective and sustainable solution to businesses. These innovative systems provide a continuous supply of high-purity nitrogen gas on-site, eliminating the need for traditional methods of gas storage and transportation. Understanding the workings of nitrogen gas generators and selecting the right system for specific processes are vital steps for businesses aiming to optimize their operations.
What is a Nitrogen Gas Generator?
A nitrogen gas generator is an air separation unit designed to produce nitrogen gas from ambient air by utilizing various separation techniques. Unlike conventional methods such as gas cylinders or liquid nitrogen dewars, which require frequent refills and logistical challenges, nitrogen gas generators offer a self-sufficient and on-demand solution. By leveraging advanced technologies, these systems extract nitrogen molecules from the surrounding air, purify them to the desired level, and deliver a continuous stream of nitrogen gas tailored to the specific requirements of industrial processes.
How does a Nitrogen Gas Generator Work?
Nitrogen gas generators operate on the principle of air separation, utilizing either pressure swing adsorption (PSA) or membrane separation technology.
Pressure Swing Adsorption (PSA): In a PSA nitrogen generator, air is compressed and passed through a series of adsorbent beds containing material such as carbon molecular sieves (CMS). Under high pressure, oxygen, moisture, and other impurities are selectively adsorbed onto the surface of the adsorbent material, allowing nitrogen gas to pass through and emerge as the product stream. The adsorption process is cyclic, with alternating adsorption and desorption stages controlled by valves, ensuring a continuous supply of high-purity nitrogen gas.
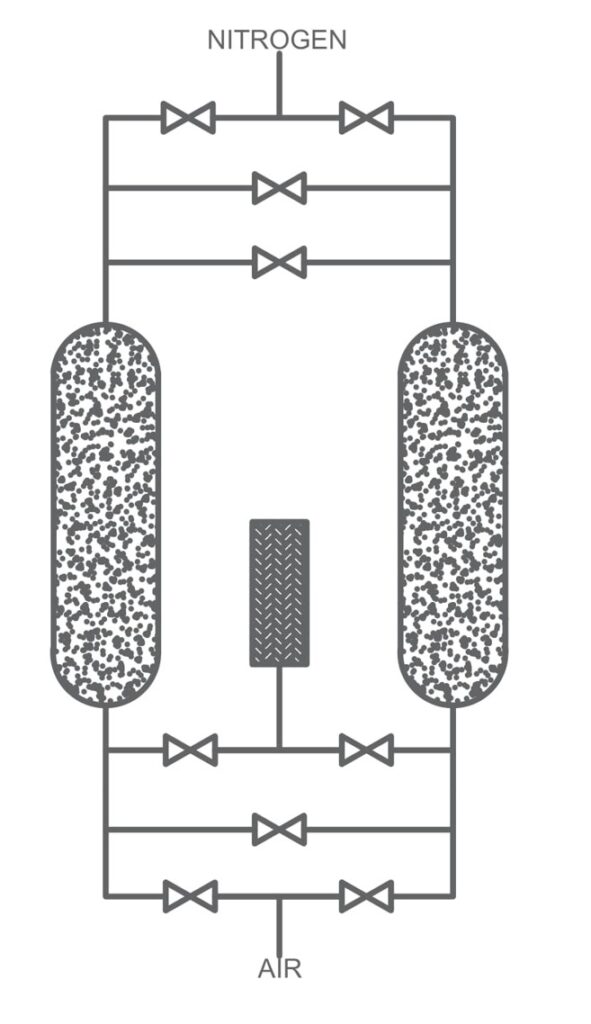
Membrane Separation: Membrane nitrogen generators utilize semi-permeable membranes to selectively permeate nitrogen molecules while blocking other components of air, such as oxygen and moisture. When compressed air is introduced into the membrane module, nitrogen molecules diffuse through the membrane pores more rapidly than oxygen molecules, resulting in a nitrogen-enriched permeate stream. By adjusting operating parameters such as pressure and temperature, membrane nitrogen generators can achieve the desired purity levels and flow rates to meet specific process requirements.
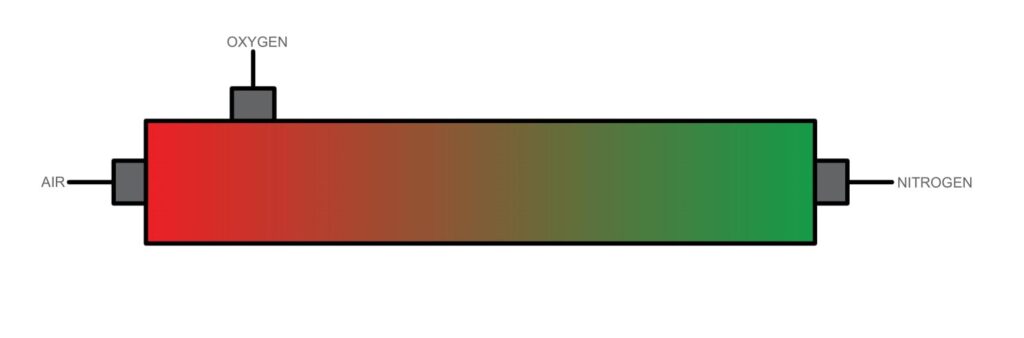
Choosing the right nitrogen gas generator for your process:
Selecting the appropriate nitrogen gas generator entails consideration of several key factors tailored to the unique needs of each business:
- Purity Requirements: Different industrial processes demand varying levels of nitrogen purity. Businesses must assess their specific purity requirements, considering factors such as oxygen concentration, moisture content, and trace impurities to ensure compatibility with the intended application.
- Flow Rate and Pressure: Determining the required flow rate and operating pressure is crucial for selecting a nitrogen gas generator that can meet the production demands of the process. Businesses should evaluate their consumption rates and peak usage scenarios to identify the optimal capacity and performance specifications required from the generator.
- Technology & Efficiency: Assessing the merits of PSA versus membrane technology is essential, considering factors such as energy consumption, maintenance requirements, and reliability. While PSA systems are well-suited for high-purity applications and fluctuating demand, membrane systems offer simplicity, lower operating costs, and compact footprint advantages.
- Footprint & Installation: Space constraints and installation considerations play a significant role in the selection process. Depending on available floor space, businesses may opt for skid-mounted, modular, or space-saving designs to optimize utilization and integration within existing infrastructure.
- Maintenance and Support: Evaluating the maintenance requirements, serviceability, and technical support offered by the nitrogen gas generator manufacturer is vital for ensuring long-term reliability and operational uptime. Businesses should seek suppliers with a proven track record of quality, responsive customer service, and readily available spare parts.
In conclusion, nitrogen gas generators represent a transformative solution for businesses seeking a reliable and cost-effective source of nitrogen gas for their industrial processes. By harnessing the principles of air separation and advanced purification technologies, these systems empower businesses to streamline operations, enhance efficiency, and reduce environmental impact. With careful consideration of purity requirements, flow rates, technology options, and support services, businesses can confidently select the right nitrogen gas generator tailored to their specific needs, unlocking a wealth of benefits and opportunities for optimization in diverse industries.
Enquire Now
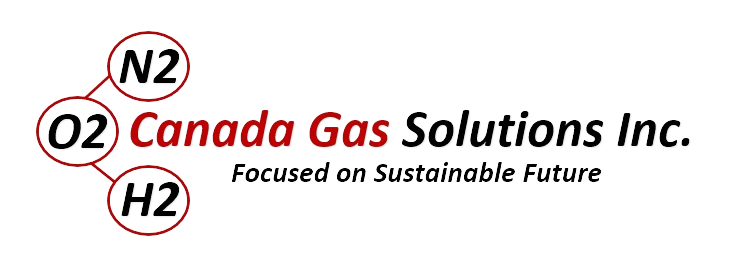