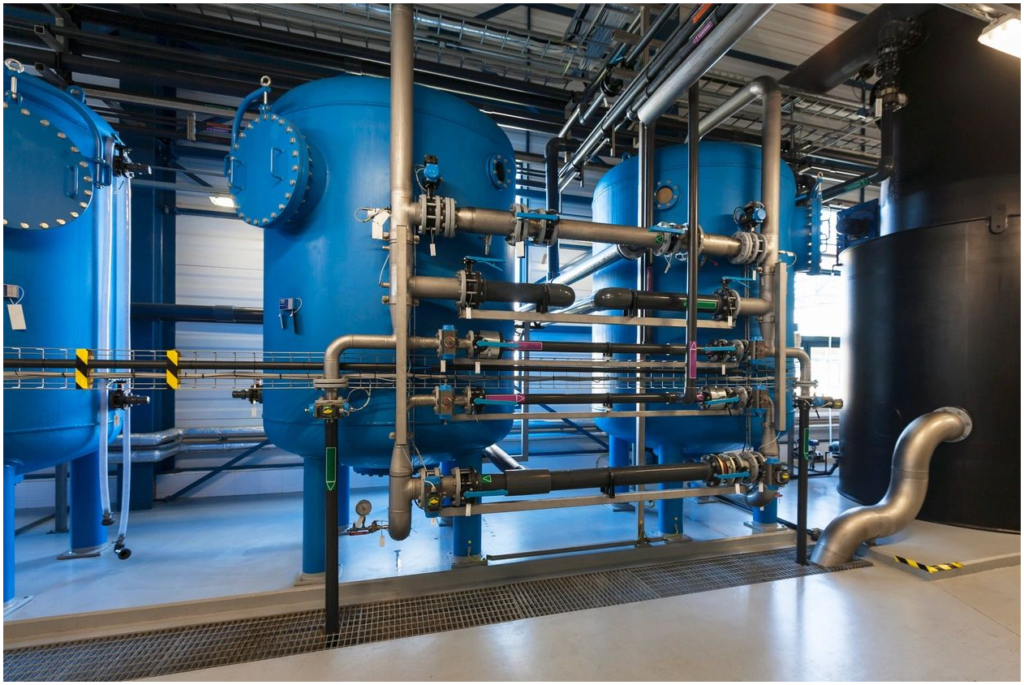
For industries relying on nitrogen or oxygen in their operations, the traditional way of sourcing these gases often involves renting high-pressure cylinders or liquid nitrogen tanks. While this approach may seem straightforward, it comes with hidden costs, inefficiencies, and logistical challenges that can be avoided by using on-site nitrogen or oxygen gas generators.
Here’s why every industrial gas consumer should compare these two options before making a decision and consider the benefits of generating gas on-site.
TAILORED TO YOUR REQUIREMENTS:
On-site gas generators produce nitrogen or oxygen precisely when and how you need it. This eliminates the risks of over-ordering or running out of gas. Whether you need a small, steady supply or a large volume for a high-demand process, on-site systems can be customized to match your operational needs. In contrast, cylinders or tanks often lock you into predetermined quantities, forcing you to pay for gas you might not use or scramble when supply runs low.
SIGNIFICANT COST SAVINGS:
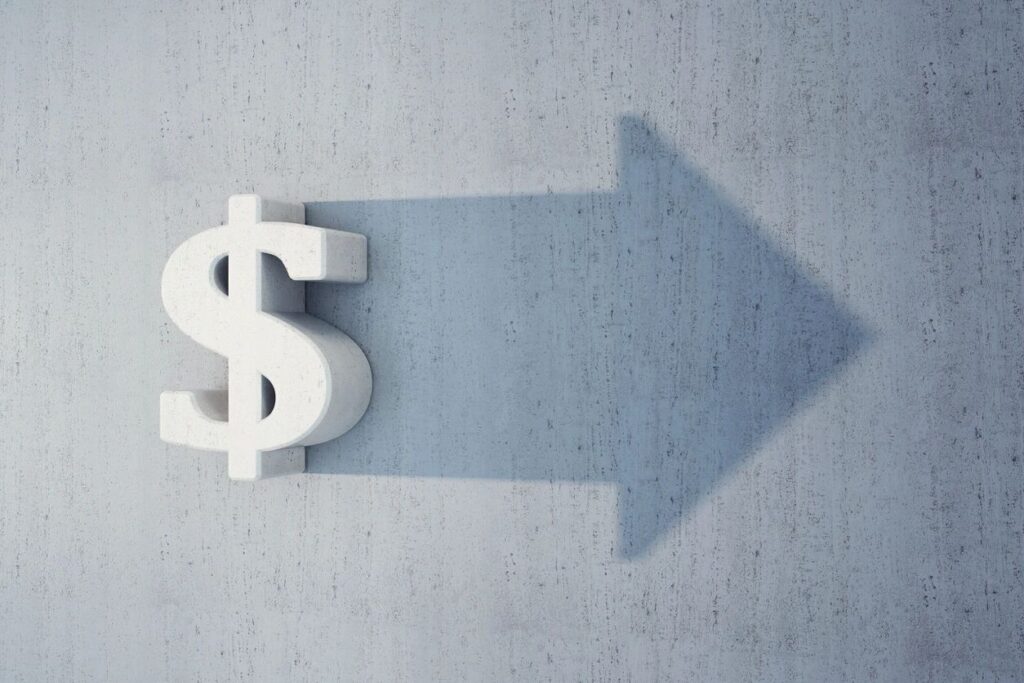
Renting gas cylinders or tanks comes with recurring costs such as:
- Delivery charges
- Cylinder/tank rental fees
- Handling and storage expenses
With on-site gas generation, these costs disappear. Once installed, an on-site system draws ambient air and generates gas on demand. Many companies report recouping their initial investment in as little as 6–24 months through reduced operational costs. After that, the savings go straight to your bottom line.
OPERATIONAL EFFICIENCY:
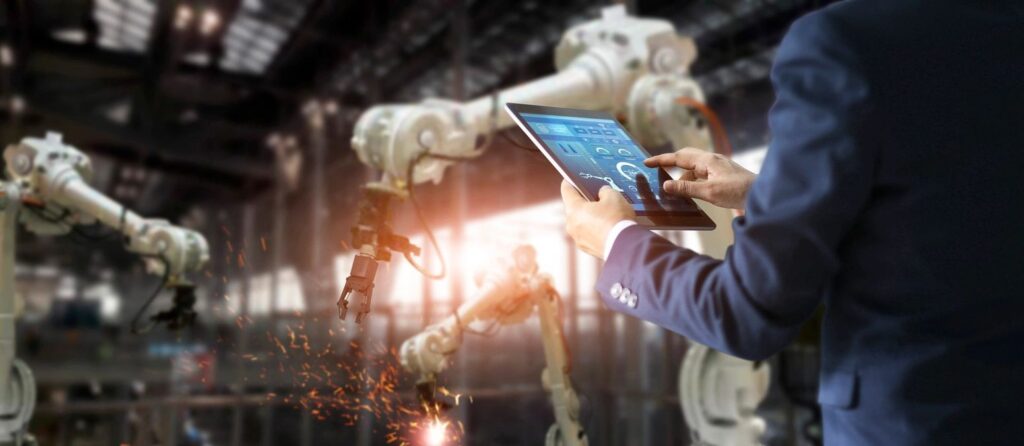
When you rely on third-party suppliers, you’re also dependent on their schedules. Delayed deliveries can disrupt your operations. On-site systems eliminate this dependency, ensuring uninterrupted gas supply whenever you need it.
Furthermore, handling high-pressure cylinders or liquid tanks requires special training and safety precautions, adding complexity to your operations. On-site systems simplify the process, reducing the risk of accidents and freeing up your workforce for more productive tasks.
ENVIRONMENTALLY FRIENDLY:
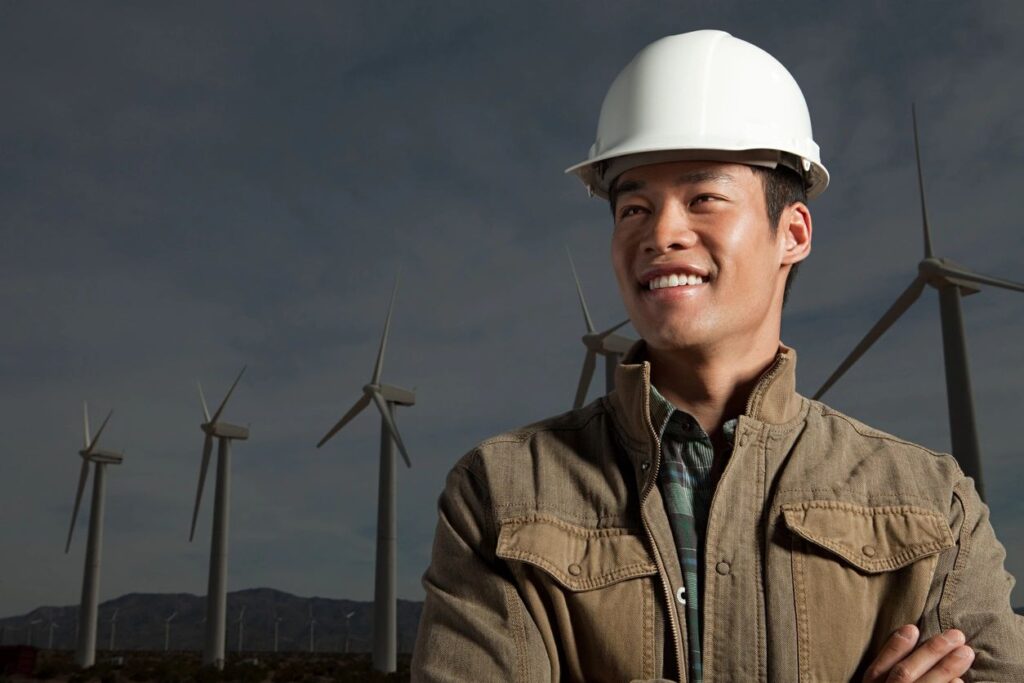
Switching to on-site gas generators reduces your carbon footprint. By cutting out the need for frequent gas deliveries and the energy-intensive liquefaction process used in tanks, your operations become significantly more sustainable.
FUTURE-PROOF INVESTMENT:
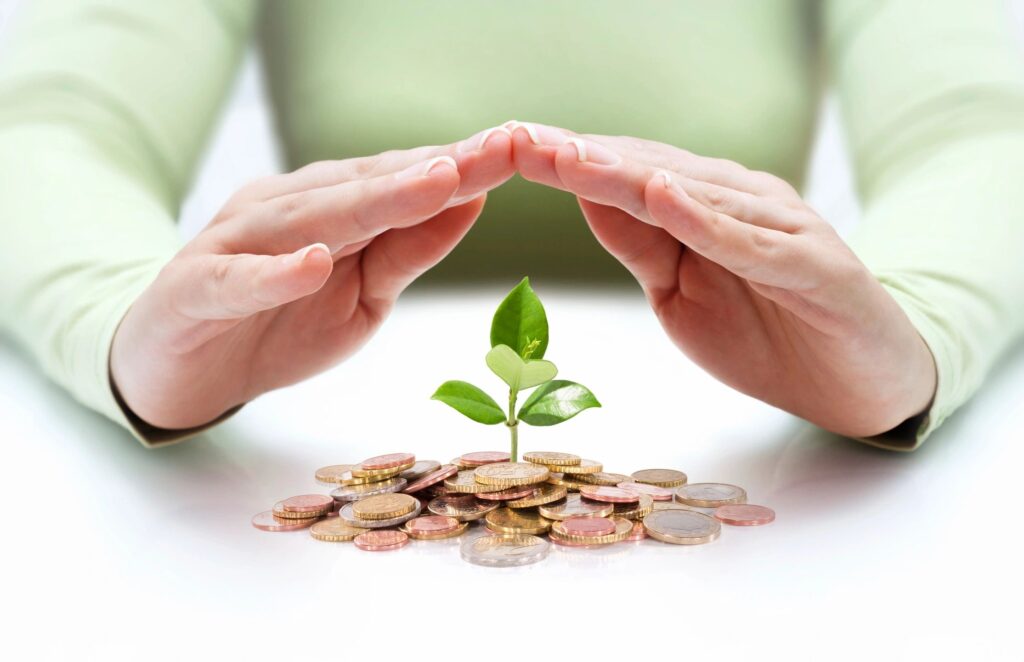
Industrial processes evolve, and so do gas requirements. On-site generators are scalable, allowing you to increase capacity as your business grows. This flexibility ensures your investment is future-proof and aligned with your long-term goals.
WHY MAKE THE SWITCH?
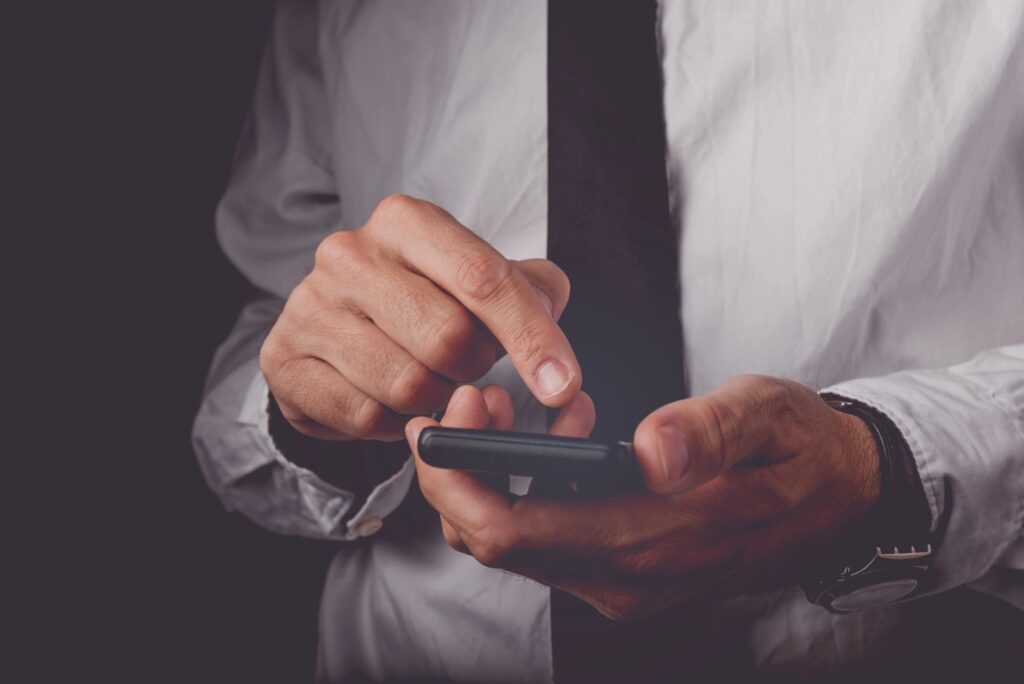
Here’s a quick comparison to illustrate the benefits:
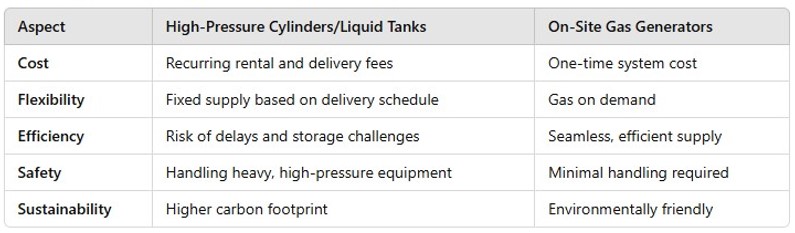
IS IT RIGHT FOR YOU?
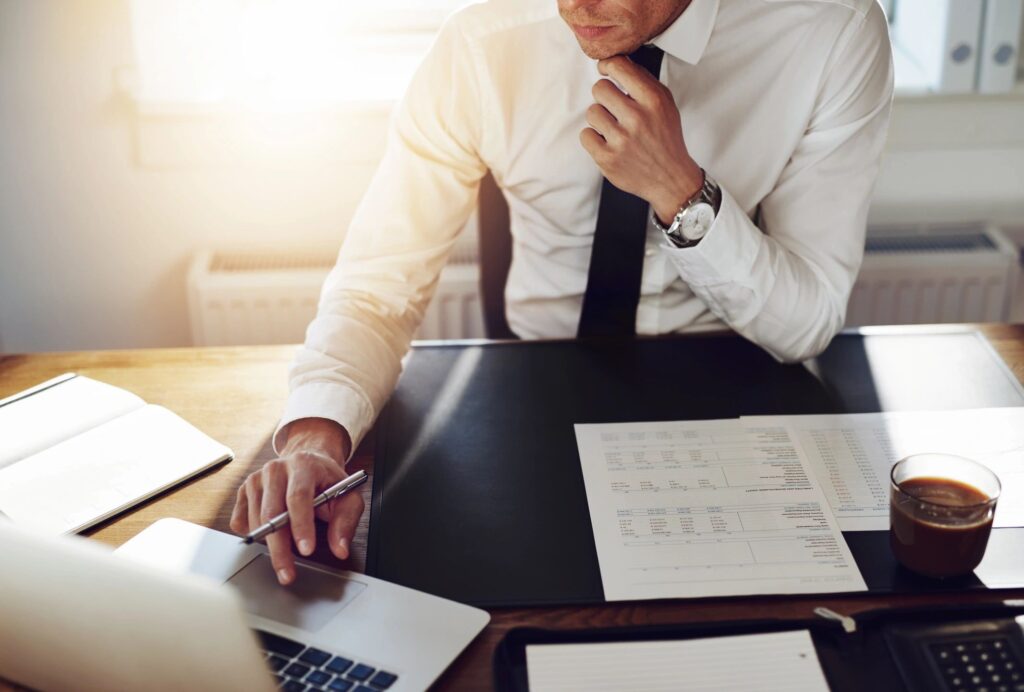
On-site gas generators are suitable for a wide range of industries, including:
- Food and Beverage
- Aquaculture
- Hospitals
- Waster Water Treatment
- Pharmaceuticals
- Metal fabrication
- Electronics
- Automotive
If your business uses nitrogen or oxygen regularly, this solution can optimize your operations, improve cost-efficiency, and reduce environmental impact.
Investing in an on-site gas generation system is a smart move for companies looking to take control of their industrial gas supply. With the ability to produce gas on demand, scale to meet your needs, and pay off the system cost within 6–24 months, this technology can revolutionize the way you operate.
At Canada Gas Solutions Inc., we understand that every business is unique. That’s why we work closely with our customers to fully understand their process requirements, including gas consumption, purity, and pressure needs. Our team designs tailored solutions that seamlessly integrate with your operations, ensuring you get the most efficient and cost-effective system for your business.
Stop relying on costly cylinders or tanks. Let Canada Gas Solutions help you explore the benefits of on-site gas generators and take the first step toward a more efficient, cost-effective, and sustainable future for your business. Reach out to us today!
Enquire Now
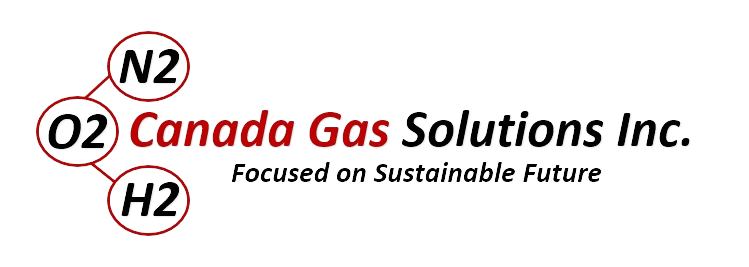