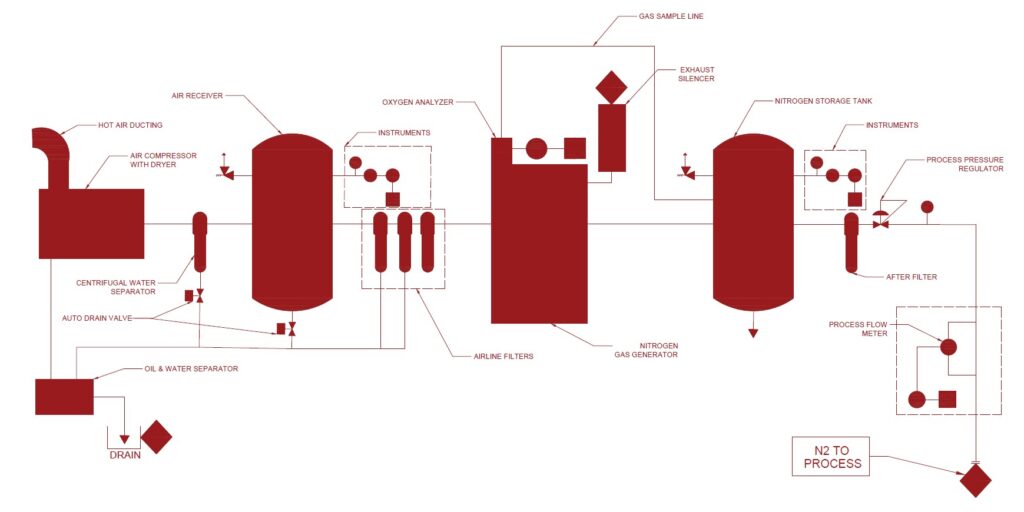
Nitrogen gas generating systems are indispensable for industries ranging from food packaging and electronics manufacturing to chemical processing and aerospace. These systems offer a cost-effective, sustainable, and reliable source of high-purity nitrogen, eliminating the need for frequent cylinder replacements or liquid nitrogen deliveries. To understand their functionality, it is essential to explore the key components that constitute these systems.
AIR COMPRESSOR: THE STARTING POINT
The process begins with the air compressor, which draws in ambient air and compresses it to the pressure required for downstream operations. Modern compressors are designed for energy efficiency, and oil-lubricated or oil-free models are preferred based on applications. Ensuring the air compressor’s capacity matches the nitrogen gas generator’s requirements is crucial for optimal performance.
AIR RECEIVER TANK
The incoming compressed air from the compressor has some pressure pulsations. To reduce these pulsations, an air receiver is installed before the air is fed to the nitrogen generator. Condensed moisture is drained out through an Auto Drain Valve located at the bottom of the air receiver.
AIR DRYER: REMOVING MOISTURE
Compressed air contains moisture, which can adversely affect the system’s performance. Air dryers remove this moisture to ensure the reliability and longevity of the equipment. Refrigerated dryers are suitable for moderate dew point requirements, while desiccant dryers are used for applications needing ultra-dry air.
Oil and Water Separator: Condensate Treatment
An oil and water separator is used to treat condensate collected from the compressed air system. This device separates oil from water, ensuring that the discharge complies with environmental regulations. Proper treatment of condensate is essential for maintaining system efficiency and environmental responsibility.
FILTRATION FOR gas PURITY
Filtration is vital for removing particulates, oil, and other contaminants from compressed air. Coalescing filters target oil and water aerosols, particulate filters capture fine particles, and carbon filters eliminate hydrocarbon vapors, ensuring the system produces high-quality nitrogen gas.
NITROGEN GENERATOR: THE CORE COMPONENT
The nitrogen generator is the heart of the system, where nitrogen is separated from compressed air. Two common technologies are employed:
- Pressure Swing Adsorption (PSA): Utilizes carbon molecular sieves to adsorb oxygen , leaving behind nitrogen. This method is ideal for high-purity nitrogen gas requirements.
- Membrane Separation: Uses semi-permeable membranes to diffuse oxygen and water vapor out, producing nitrogen. Membrane systems are compact and suited for low to moderate purity levels.
NITROGEN RECEIVER TANKS: ENSURING STEADY SUPPLY
A low pressure nitrogen gas generating systems typically include two receiver tanks:
- Air Receiver Tank: Buffers fluctuations in demand and ensures consistent airflow to the generator.
- Nitrogen Receiver Tank: Stores generated nitrogen gas, providing a steady supply to applications.
ADVANCED CONTROL SYSTEMS
Modern systems feature control mechanisms to monitor and manage parameters like pressure, flow rate, and purity levels. Programmable Logic Controllers (PLCs) enable automation and remote monitoring, while user-friendly touchscreen interfaces simplify operation.
PIPING AND VALVES: SEAMLESS INTEGRATION
High-quality piping and valves are essential for efficient airflow. Using leak-proof fittings and corrosion-resistant materials ensures the system’s durability and effectiveness.
PRESSURE REGULATION
A pressure regulator maintains the correct delivery pressure of nitrogen, safeguarding sensitive equipment and ensuring consistent application performance.
oxygen ANALYZER: ENSURING STANDARDS
Oxygen analyzers verify the concentration of nitrogen, ensuring it meets required standards for specific industrial applications.
OPTIONAL ACCESSORIES
To enhance functionality, systems may include optional accessories such as gas flow meters to monitor nitrogen usage, alarms for low purity or low/high-pressure issues, and remote monitoring systems for real-time data access.
Nitrogen gas generating systems are sophisticated assemblies of interconnected components designed to deliver high-quality nitrogen efficiently and reliably. Each component plays a pivotal role in the system’s overall functionality, making it essential for businesses to understand these building blocks. By doing so, they can select and maintain a nitrogen generation solution tailored to their unique needs.
At Canada Gas Solutions, we specialize in providing perfectly designed nitrogen gas generating systems tailored to meet specific customer requirements. With our expertise in selecting and sizing components, we ensure that our systems are efficient, reliable, and optimized for the unique needs of each application. Let us help you achieve a seamless and sustainable nitrogen generation solution.
Enquire Now
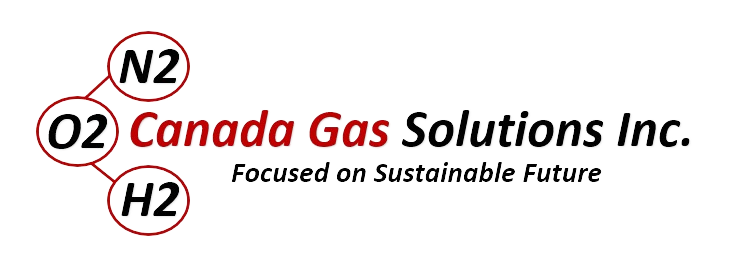